Six Sigma Case Study: Ford Motors
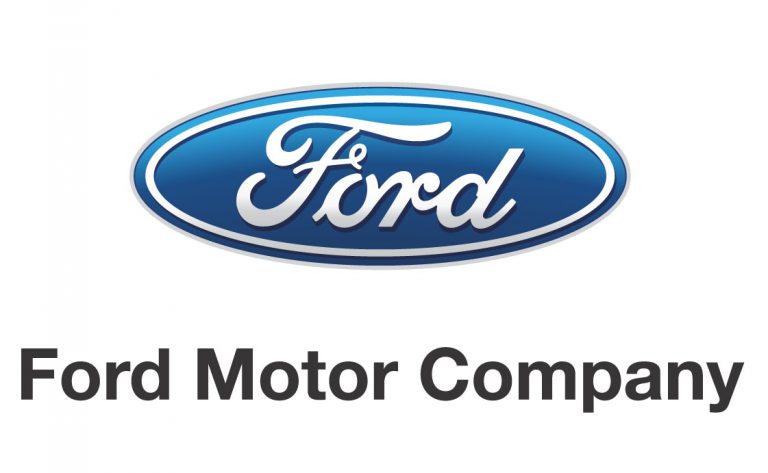
The Ford Motor Company is one of America’s, and the world’s, largest and most successful automakers. Named after its founder Henry Ford, the company is known for its innovative and dynamic approach to manufacturing. Henry Ford pioneered and employed such manufacturing concepts as standardization, assembly lines, which came to be known as Fordism. He also paid his workers a living wage, allowing them to purchase the very products they made. Products like his famous Model T.
Ford was a visionary man. He saw the necessity of breaking down complex tasks into simpler procedures, using specialized tools, and interchangeable parts. While Ford’s assembly line was a revolutionary achievement, his work grew from solidified ideas, with an eye for continuous improvement. Ford looked at established modes and broke them down into their core components, before building them back up again. He strove to take existing processes and always make them more functional, efficient, and effective. There were many advantages to Ford’s ideas. Namely, the significant decrease in costs of production, radically simplifying the labor process and reducing required the workforce.
Learn More About Lean Six Sigma Online Program
But how are Six Sigma and all its related approaches, like Lean and Kaizen, related to Ford? As you may know, Ford is a company known for its high quality. The company has pledged to utilize innovative products and use Total Quality Management to accomplish its goal of Quality Is Job 1. JD Power and Associates ranked Ford as one of the leading high-quality automakers, but Ford has come a long way in the last few decades. Today we examine just how the Ford Motor Company used Six Sigma to transform its processes and achieve its success.
Why Was Six Sigma Necessary for Ford?
There are four core factors behind Ford’s Six Sigma initiative. These are:
- Cost reduction. Ford’s old production process was surprisingly costly. By introducing Six Sigma, they were no longer using resources that were not necessary.
- Improving quality. Ford has always been known for their quality products, but event heir standards slip from time to time. While, for most companies, a mere 99% quality level is considered acceptable, this lets through a surprising amount of defect. As much as 20,000 instances of defect. Six Sigma espouses that only 99.99966% (and up) is ideal. This percentage limits the number of defects per million to just seven As such, Ford made some great astonishing strides in quality improvement using Six Sigma.
- Poor customer satisfaction rates. Satisfying customer demand is as critical to success as leveraging it. Many of these issues link to one another, as multiple instances of defect are likely to add up to a defective product. This will inevitably dissatisfy the customer which is why Ford chose to implement Six Sigma, to streamline their processes, and improve production issues. All of which adds up to a more productive company and happier customers.
- Lowering environmental impact by reducing solvent consumption. Six Sigma is an extremely green philosophy, and Ford uses it to make some great changes in their environmental awareness. Ford’s consumption of vital resources proved very costly in the long-term. But by committing to a green work culture with Six Sigma, they reduced costs, increased quality, and improved customer satisfaction.
Ford’s Approach to Six Sigma
The Ford Motor Company began using Six Sigma strategy in the late nineties. Their goal was to become a fully-fledged consumer products company and not just another automobile manufacturer. Additionally, they wished to enhance the quality of their products and to improve their customer satisfaction rates. Their approach towards achieving these goals they referred to as Consumer-driven Six Sigma. Furthermore, Ford was the world’s very first automaker company to implement Six Sigma methodology into their business operations on a large scale.
One of the most pressing problems facing Ford at the time was the 20,000 plus opportunities for defects that came with manufacturing cars. Despite the company’s prior history of quality control and innovation, some defects inevitably slipped through their fingers. Following this revelation, they achieved substantial improvements using Six Sigma. Their aim was to reduce their defect rate to only a single defect per every 14.8 vehicles, and they succeeded. Furthermore, this also satisfied their goal of enhancing customer satisfaction. In Six Sigma, even the smallest change can have a ripple effect, helping to change other processes and move towards continuous improvement.
Obstacles for Ford’s Six Sigma Initiative
Despite its success, there were several obstacles in the way of Ford’s Six Sigma implementation. These are:
- Employee commitment. As is often the case, many employees at Ford, including top-level and senior management, initially viewed Six Sigma with skepticism. This meant a lack of commitment was present from the beginning, proving a major cause of concern for Ford’s Six Sigma implementation. The time constraints, on top of this, made it difficult to put its 350 top leaders through weeks of training.
- Time, Money, Productivity. Furthermore, along with a lack of commitment, key resources like time and money meant employee training was often difficult. The lack of commitment also led to a lack of productivity.
- Data needs. Finally, Ford was new to Six Sigma and poorly equipped to follow through with its Six Sigma initiative. Six Sigma, of course, relies on vast amounts of data to This meant that Ford needed to create and implement new measurement systems to tackle the needs of Six Sigma. Only then was it able to provide any great benefit for the company.
Ford’s Six Sigma Successes
Ford’s use of Six Sigma methodology, while it did provide some road bumps, enabled them to eliminate more than $2.19 billion in waste over the last decade and a half. They solved this problem by applying Lean Six Sigma techniques, such as a data-driven problem-solving process, to devise solutions to waste issues. Moreover, the company’s methodologies for quality improvement and waste elimination saw a staggering impact on the company’s operations. Ford’s Consumer-driven Six Sigma has saved them over a billion dollars worldwide, helping complete almost 10,000 improvement projects since the early 2000s. Regarding customer satisfaction, Ford managed to increase their percentage by five points. We may go as far as to say that Six Sigma saved Ford from its deep-rooted problems. These issues include inadequate productivity, poor use of resources, low customer satisfaction, and environmental unfriendliness.
Contact us and find out how we can positively help you plan and change the culture and operations of your organization. We offer Six Sigma Green Belt and Six Sigma Black Belt training programs, as well as a Six Sigma Master Black Belt program.
SixSigma.us offers both Live Virtual classes as well as Online Self-Paced training. Most option includes access to the same great Master Black Belt instructors that teach our World Class in-person sessions. Sign-up today!
Virtual Classroom Training Programs Self-Paced Online Training Programs