Back to Basics: DMAIC, What Is It and How to Use It?
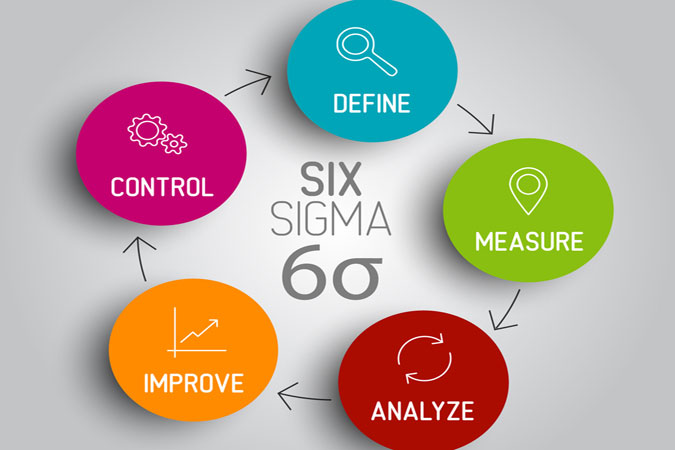
What Is DMAIC?
When studying Six Sigma at any certification level, the most important method you will learn is DMAIC. This acronym stands for Define, Measure, Analyze, Improve, and Control. Furthermore, it helps solve problems where the solution is not always clear. Many time when using Six Sigma, your goal is to improve a business process. This could mean increasing the efficiency, reducing waste, or deterring production defects. But, how exactly do you accomplish these goals? DMAIC is your answer!
D – Define
The first step in DMAIC is ‘Define’. At this stage, your goal is to define the problem. What are you trying to solve by implementing Six Sigma? What criteria must you analyze and how will you turn your data into a quantifiable form? Likewise, this step helps distinguish the “vital few” from the “trivial many” in terms of critical to quality characteristics (CTQs). In the end, you will have a map of the process you need to improve.
M – Measure
Now that you know what characteristics of you project you want to analyze, you must measure them. Typically, the most experience Belt (usually a Black Belt or higher) will assess the ability to measure these variables. The project must be clearly outlined and assessed to define the Key Process Steps and each Key Input. From here, you can determine whether the CTQs are being influenced and if there is a connection to the process’ errors. One key thing to remember is to measure with the correct metrics! Not doing so will provide inaccurate data.
A – Analyze
At this step, the project team will use analysis to find reasons for the errors that are occurring. Likewise, members will also use this step to see how far the project currently is from the overall goal and how to reduce this gap. Project members will discover why deficiencies occur by altering variables and recording their responses. Although this step may require more time than others, it’s likely the most valuable in the whole process.
I – Improve
Now that you know what caused your process’ errors, it’s time to solve them! Using the data from the previous step, your team will now find innovative ways to correct and improve your process. Often, this step is seen as the most challenging. On the contrary, ‘Improve’ gives you the chance to try new innovations and improve upon a proven process for the better.
C – Control
At the last step in DMAIC, it’s time to put the changes into place. With ‘Control’, your job is to maintain the success you gain from the four prior steps. The changes you made, whether in the process, with management, or both must be held constant to ensure the same results. Additionally, groups will create a specific operating procedure for the specific process that includes the changes made. Ultimately, this stage determines how well you have performed the DMAIC method.
One often overlooked step is ‘Synergize’. This step ensures that you share your findings with the rest of the organization. When your Six Sigma team shares the changes made with the whole organization, everyone can learn and benefit from the results.
SixSigma.us offers both Live Virtual classes as well as Online Self-Paced training. Most option includes access to the same great Master Black Belt instructors that teach our World Class in-person sessions. Sign-up today!
Virtual Classroom Training Programs Self-Paced Online Training Programs