Kaizen – Pursuing Continuous Improvement
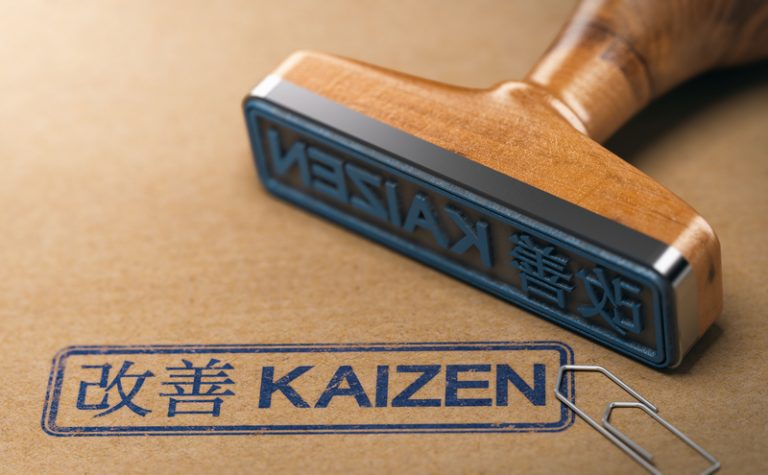
Kaizen is a term that you’ll constantly hear in Lean Six Sigma circles. However, not many people know what it means. That is because the term itself does not convey any obvious meaning. One would not be blamed for thinking it is some fancy new process, organization or machine.
However, the concept of Kaizen is not hard to understand in terms of what it is and what it tries to achieve. On top of that, it is a fundamental concept for any organization to understand and implement, especially if they take process improvement seriously.
What is Kaizen?
To put it simply, Kaizen means “continuous improvement.” The reason people prefer calling it Kaizen is because the philosophy came from the Japanese after WWII. It is a combination of two Japanese terms “kai” and “zen,” which mean “change” and “good,” respectively.
In a nutshell, Kaizen is a philosophy that encourages continuous improvement (gradual change for the better) of processes. Through Kaizen, it is believed that organizations will become more efficient and profitable over time. It was popularized by Toyota in the 1980s and has now become a global phenomenon.
Normally, we think in terms of “don’t fix what isn’t broken.” But Kaizen forces us to think in terms of “if it can be improved, then it should be improved.” Kaizen is about doing it better to compete with those that are also doing it better and outdo those that aren’t.
5 Key Elements of Kaizen
There are five important tenets when it comes to Kaizen. These are:
- Teamwork: Kaizen should include everyone in the organization – that means employees at all levels should be involved. Everyone should work together to benefit the organization through timely collaboration, whether it is exchanging information or completing tasks.
- Personal discipline: Kaizen demands that everyone involved practice self-discipline at all times. They should be organized, manage their time efficiently, use resources wisely, do quality work and so on. No one can contribute to the success of the organization without personal discipline.
- Improved morale: Upper management should focus on keeping employees motivated because that is when they will do their best work. They are several tools that upper management can use to drive motivation. These include:
- Offering performance-based incentives.
- Not micromanaging employees but fully trusting them and their work.
- Giving recognition to the best performers. For example, giving one of them the title of “Employee of the month.”
- Offering fun breaks from the monotony of work, such as fun days, retreats or picnics.
- Offering opportunities for further career development, such as training, mentorship, coaching and promotions to leadership roles.
- Quality circles: These involve employees at different levels of the organizations meeting to share ideas and solve problems. The main goal here is to improve the quality of work.
- Suggestions for Improvement: Every employee involved should have the freedom to suggest improvements. It doesn’t matter what level they are in the organization, their suggestions should be given the time they deserve. Everyone’s opinion is valued and considered.
Conclusion
Kaizen helps organizations in their pursuit of continuous improvement. Now that you know what it is and its key elements, the term has been demystified. When done right, Kaizen can make an organization highly competitive and profitable.
SixSigma.us offers both Live Virtual classes as well as Online Self-Paced training. Most option includes access to the same great Master Black Belt instructors that teach our World Class in-person sessions. Sign-up today!
Virtual Classroom Training Programs Self-Paced Online Training Programs